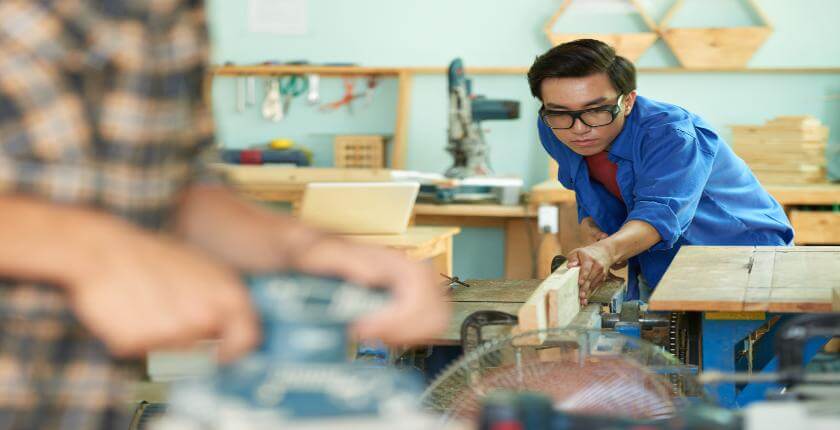
Refactory Services in Grimsby
Enquire Today For A Free No Obligation Quote
At Refractory Services in Grimsby, we provide expert refractory installation, repair, and maintenance solutions across the UK.
Considering the extreme conditions present in many industrial processes, properly installed refractory systems are essential for operational safety, energy efficiency, and regulatory compliance.
Routine maintenance and professional installation play a vital role in preventing downtime and extending equipment life.
Get a tailored refractory solution for your operation – request your quote in Grimsby now.
What Do Refractory Services in Grimsby Include?
Refractory services in Grimsby cover the design, installation, repair, and maintenance of heat-resistant linings for equipment exposed to extreme temperatures.
Typical works involve bricklaying, gunning, casting, ramming, and ceramic fibre lining depending on the application.
Materials are selected based on the thermal, chemical, and mechanical demands of the process environment.
Technicians also carry out demolition of damaged linings, anchor system installation, and drying or curing as needed.
To ensure performance, all work is executed according to industry standards and tailored to the specific requirements of each furnace, kiln, or reactor.
How Much Do Refractory Services Cost in Grimsby?
The cost of refractory services in Grimsby is from £2,000 to over £50,000.
Small repairs or patchwork on boilers may cost between £2,000 and £8,000, while full furnace re-linings or kiln rebuilds can exceed £20,000 due to extended labour, scaffolding, and refractory material costs.
Final pricing is fully dependent on project size, access, material type, and system complexity.
Since each project has unique operational and technical demands, accurate costs are provided following a site survey or engineering review.
What Are the Benefits of Professional Refractory Services in Grimsby?
Refractory services maintain heat-resistant linings, improve furnace efficiency, and reduce industrial downtime.
The benefits of professional refractory services include:
- Protects equipment from extreme temperatures, abrasion, and chemical attack
- Improves energy efficiency and thermal performance of process systems
- Reduces unplanned downtime and costly emergency repairs
- Supports compliance with industry safety and environmental regulations
- Extends operational life of furnaces, kilns, boilers, and incinerators
What Industries Use Refractory Services?
Refractory services Grimsby are used across multiple sectors including steel and foundry, glass, cement, petrochemical, waste-to-energy, biomass, ceramics, and power generation.
These industries rely on refractory linings to protect their equipment from molten metals, chemical slag, thermal cycling, and abrasion.
High-temperature environments such as rotary kilns, ladles, incinerators, and boilers all require refractory maintenance to function safely and efficiently.
To meet sector-specific standards, each project is customised to process conditions, service temperature, and atmosphere exposure.
Why Is Refractory Maintenance Important in Grimsby?
Refractory maintenance is essential to prevent equipment failure, maintain process integrity, and ensure worker safety in high-temperature operations.
Worn or cracked linings can lead to hot spots, structural damage, gas leakage, or complete shutdowns.
Since undetected refractory degradation often results in catastrophic equipment failure, regular inspections and preventive maintenance are critical.
Well-maintained linings improve thermal efficiency and reduce fuel consumption.
To maximise equipment lifespan and avoid unplanned outages, consistent maintenance is a cost-effective investment.
What Are the Signs That Refractory Lining Needs Repair?
Common signs include visible cracks, spalling, excessive wear, hot spots, deformation, and decreased performance efficiency.
In some cases, leaking gases or material buildup can also indicate refractory failure.
Thermographic imaging or ultrasonic testing may reveal subsurface issues not visible to the eye.
Operators may also notice changes in heat retention or increased fuel use.
Since small issues can escalate quickly under high temperatures, any suspected damage should be evaluated immediately.
Do You Work with All Refractory Material Types?
Our services in Grimsby cover the full spectrum of refractory materials, including firebrick, dense castables, insulating castables, ceramic fibre, plastic refractories, and precast shapes.
Material selection is based on process temperature, mechanical loading, chemical exposure, and thermal cycling characteristics.
For example, firebrick is commonly used in kiln walls, while fibre modules may suit heat exchangers or duct linings.
To ensure durability and compliance, each application is matched with the correct refractory formulation and installation method.
How Long Does Refractory Installation Take in Grimsby?
Refractory installation in Grimsby typically takes between two days and several weeks depending on the scope, structure size, and material type.
Simple patch repairs or gunning work can be completed within one to three days.
Full re-linings of furnaces, rotary kilns, or incinerators may require one to three weeks to complete, including demolition, installation, and drying.
The curing or sintering process may also add time to total turnaround.
To minimise downtime, we work within planned shutdown schedules and optimise installation sequencing.
Are Refractory Services in Grimsby Available During Plant Shutdowns?
Refractory services in Grimsby are often scheduled during plant shutdowns or maintenance turnarounds to minimise operational disruption.
Teams are mobilised in advance, and project timelines are tightly coordinated to meet shutdown windows.
Materials are staged, and work is phased to ensure safe and efficient completion.
For clients with annual shutdown cycles, we offer inspection services beforehand to prioritise repairs.
To ensure a seamless shutdown process, all safety protocols and documentation are prepared prior to mobilisation.
Can You Provide Emergency Refractory Repairs?
Emergency refractory repair services are available for unplanned failures, breakdowns, or safety-critical incidents.
These services include 24/7 call-outs, on-site assessments, and rapid deployment of skilled crews and materials.
Repairs are prioritised based on severity, process risk, and operational impact.
For high-temperature equipment, temporary patching may be followed by full lining restoration during the next shutdown.
To reduce downtime, response teams are equipped for fast execution under pressure.
Do You Offer Refractory Inspection and Testing in Grimsby?
Inspection and testing services in Grimsby include visual assessments, thermography, hammer testing, core sampling, and ultrasonic testing to evaluate refractory integrity.
These inspections detect hidden cracks, material thinning, and thermal inconsistencies.
Testing is often performed during shutdowns or as part of a condition-monitoring program.
Reports include detailed findings, photographs, wear mapping, and repair recommendations.
To support asset management, inspections can be conducted annually or before major maintenance works.
Can You Design Custom Refractory Solutions?
Custom refractory design is available for new installations, system upgrades, or non-standard geometries.
Our engineers develop layouts based on thermal modelling, service conditions, and anchoring requirements.
Drawings and specifications are produced to meet client and industry standards.
We also manufacture precast blocks or shaped linings for bespoke applications.
To ensure successful outcomes, we collaborate with plant engineers, consultants, and OEMs from design to execution.
What Safety Measures Are Taken During Refractory Work?
Refractory projects follow strict safety procedures including confined space protocols, hot work permits, PPE compliance, and full risk assessments.
Site-specific method statements and rescue plans are implemented for enclosed or elevated workspaces.
Crew members hold qualifications in first aid, confined space entry, abrasive wheel use, and safe refractory handling.
To maintain a safe environment, daily toolbox talks and supervisor checks are performed on every job.
Do You Work on Boilers and Incinerators?
Refractory linings for boilers, waste incinerators, and energy recovery systems are a core part of our service offering.
These systems face aggressive thermal cycling, slag formation, and chemical attack, making refractory durability critical.
Services include removal of old linings, anchor installation, casting or fibre lining, and thermal dry-out.
For waste-to-energy and biomass facilities, high-resistance materials are used to counter chemical wear.
What Is the Typical Lifespan of a Refractory Lining?
The lifespan of a refractory lining depends on its material type, operating conditions, and maintenance schedule.
Standard firebrick linings may last three to five years in moderate environments, while high-performance castables in aggressive conditions may require repair or replacement within two years.
Well-maintained linings with proper installation can exceed expected lifespans.
To maximise service life, regular inspections and targeted repairs are essential.
Performance data from prior maintenance also helps inform predictive schedules.
How Do I Get a Free Quote for Refractory Services?
To get a free quote for refractory services, simply send us a message through the contact page with details about your site, equipment, and service needs.
Our team in Grimsby will assess your requirements and provide a tailored, no-obligation quotation.
Get in touch today to schedule your assessment and ensure your high-temperature systems stay protected and compliant.
Find More Info
Make sure you contact us today for a number of great refactory services in Grimsby.
For more information on refactory services in Grimsby DN31 1, fill in the contact form below to receive a free quote today.
★★★★★
“Their refractory services were crucial during our kiln relining project. The team was efficient, safety-conscious, and delivered outstanding results.”
Stuart Holleran
Lincolnshire
★★★★★
“We’ve worked with several refractory contractors, and this team stands out for quality and reliability. Downtime was minimal, and their workmanship was solid.”
Monica Threlfall
Lincolnshire